Infrastructure
Infrastructure Excellence Hub
At Siddheshwar Technoforge, our comprehensive infrastructure includes a cutting-edge laboratory, advanced tooling shop, state-of-the-art forging facility, and a precision machine shop. This integrated setup ensures seamless processes and superior quality throughout our manufacturing journey.
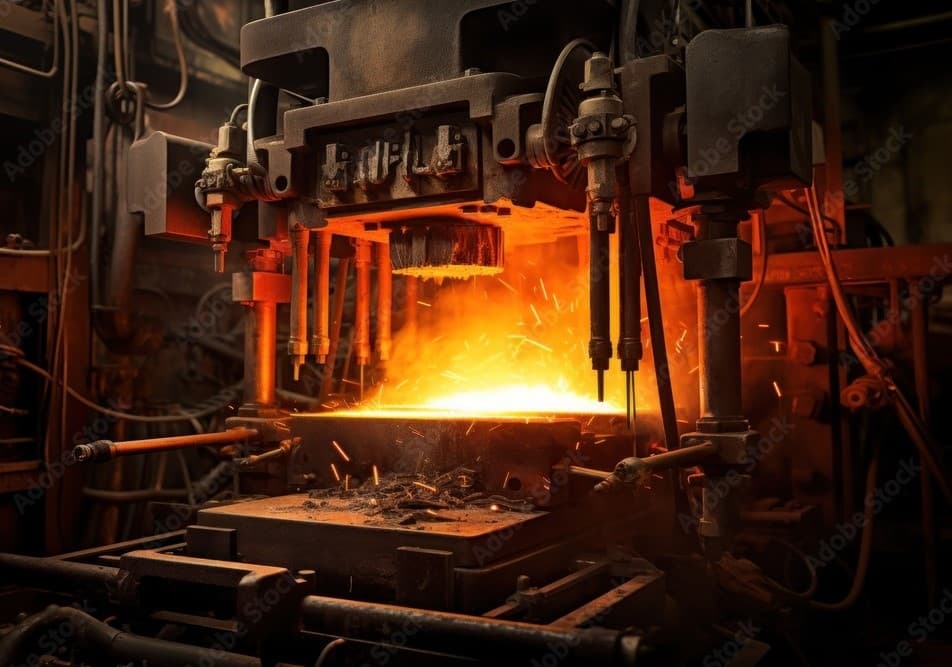
Friction Drop[Hammer - 1.5 MT, 1 MT]
Our commitment to precision forging is exemplified by the installation of our Friction Drop Hammer. This advanced machinery, with a capacity of 1.5 and 1 metric ton, is a cornerstone in our forging facility, offering exceptional efficiency and accuracy in shaping metal components.
The Friction Drop Hammer's robust design and controlled impact force enable us to achieve unparalleled precision in the forging process, ensuring the production of high-quality components for diverse industries.
The Friction Drop Hammer stands as a testament to our dedication to cutting-edge technology. Its seamless integration into our facility enhances our forging capabilities, allowing us to meet the stringent demands of clients in sectors such as Agriculture, Railway, and Automotive.
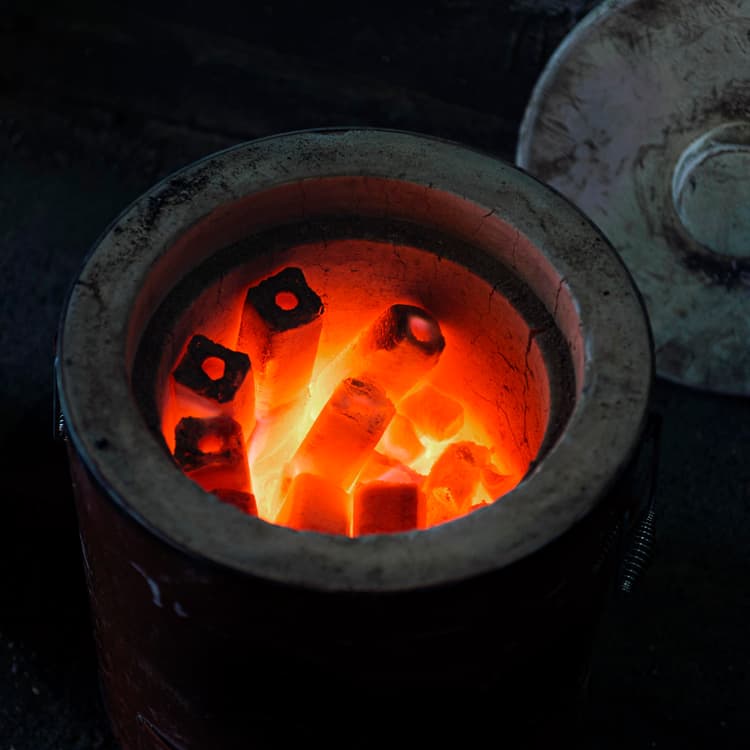
Oil Fired Furnace[Loading Capacity: 5 MT]
We proudly utilize a Fix Industrial Oil Fired Furnace with a substantial material loading capacity of 5 metric tons. This high-performance furnace is a key component of our advanced manufacturing infrastructure, ensuring efficient and precise heating for the forging process. With its robust design and cutting-edge technology, our 5 MT Fix Industrial Oil Fired Furnace plays a crucial role in maintaining optimal temperature conditions, contributing to the production of top-quality forged components across a spectrum of industries.
Engineered for reliability and efficiency, our Fix Industrial Oil Fired Furnace exemplifies our commitment to delivering superior forging solutions. Its substantial material loading capacity enhances our production capabilities, allowing us to meet the diverse needs of clients in sectors

Laboratory
Our well-equipped laboratory is furnished with cutting-edge tools, including a powerful Microscope with 1000X magnification and Image Analyzer. Complementing our advanced testing capabilities, we employ HRC Tester, Brinell Hardness Tester, and an MPI Machine in-house. These sophisticated instruments empower us to conduct meticulous examinations of material properties, ensuring the highest standards of quality in our forged components. Our laboratory serves as a critical hub for evaluating chemical compositions, inclusion ratings, and mechanical characteristics such as tensile strength, yield strength, elongation, and impact resistance.
In addition to our in-house testing, we places a premium on external validation. We collaborate with NABL Accredited Labs (National Accreditation Board for Testing and Calibration Laboratories ) to conduct rigorous examinations, including chemical analysis to assess composition and inclusion rating. Furthermore, our mechanical analysis at these external facilities evaluates critical factors like tensile strength, yield strength, elongation, and impact resistance. This dual approach underscores our commitment to delivering precision and reliability in every forged product, meeting or exceeding industry standards

Tooling Shop
In our Tooling Shop, we boast advanced design capabilities to ensure the highest precision in forging processes. Our expert team employs 2D drafting using AutoCAD for meticulous planning and visualization. Additionally, we harness the power of'Unigraphics NX' for comprehensive 3D solid modeling, allowing us to create intricate and accurate designs.
From the initial concept to the final product, our tooling shop is equipped to handle the full development of forging dies, trimming dies, and punches, demonstrating our commitment to excellence in tooling and design innovation.
Beyond the realm of traditional tooling, our Tooling Shop is a hub of innovation. Our design process is driven by a relentless pursuit of excellence, ensuring that each tool we develop is not just a product but a testament to precision craftsmanship. With an unwavering commitment to pushing the boundaries of design and engineering, our tooling capabilities stand as a cornerstone in our pursuit of delivering forging solutions that redefine industry standards
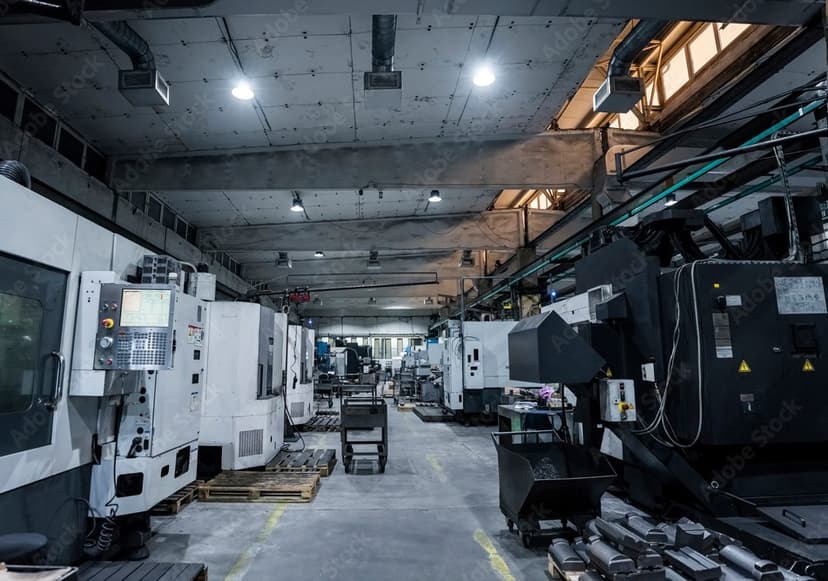
Mechanic Shop
In our advanced Machine Shop, we boast a robust production capacity of 1,00,000 pieces per month, showcasing our dedication to meeting high-volume manufacturing demands. Our flexible supply conditions offer components in pre-machined, fully machined, and ready-for-installation states, providing tailored solutions to diverse client needs. Our internal processes encompass turning and milling/drilling, ensuring precision in crafting components to meet the most stringent specifications.
Equipped with cutting-edge machinery, the Machine Shop features 20 CNC Turning machines, 6 CNC Milling machines (3/4/5 Axis), and 5 Conventional Lathes. This state-of-the-art setup allows us to execute intricate machining processes with efficiency and accuracy. Whether it's turning for cylindrical components or multi-axis milling for complex geometries, our skilled team leverages the latest technology to deliver superior results. The Machine Shop stands as a testament to our commitment to advanced manufacturing, providing components that consistently meet the highest industry standards.
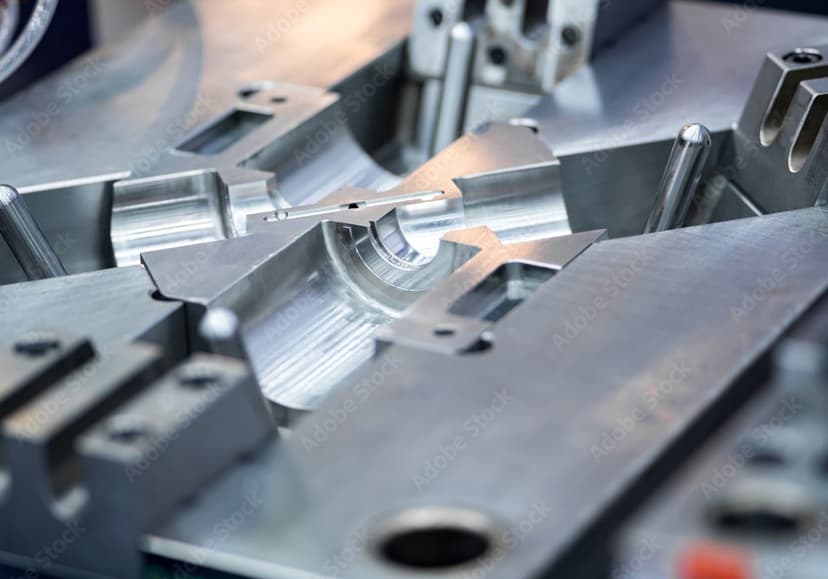
Die Shop
Our die creation unit is staffed by a team of highly skilled engineers and craftsmen who possess a wealth of experience in tooling and die-making. Leveraging cutting-edge software and manufacturing techniques, they meticulously craft dies that meet the exacting specifications required for forging a wide range of materials.
Our dedication to quality extends beyond the design phase. We employ the latest machining technologies and premium-grade materials to manufacture dies that can withstand the rigors of high-volume production while maintaining tight tolerances and surface finish requirements.